A Comprehensive Guide to Industrial Belts: Types, Materials, and Applications
Industrial belts are essential components in modern industrial production, widely used in various machinery driven by electric motors and internal combustion engines to perform important functions such as power transmission and material conveying. There are many types of industrial belts, which can be classified based on different materials, structures, and applications. Below, we will discuss the main types of industrial belts and their characteristics in detail.
Classification by Material
1. Rubber Belts
Rubber belts are one of the most common types of industrial belts, made from natural or synthetic rubber. They offer excellent flexibility and wear resistance, making them suitable for various complex working environments. Rubber belts are widely used in industries such as power generation, metallurgy, and chemicals, especially in conveyor systems like coal conveyors, mining conveyors, and more. Depending on the specific requirements, rubber belts can be further divided into special-purpose belts such as oil-resistant, acid-alkali-resistant, and high-temperature-resistant belts.
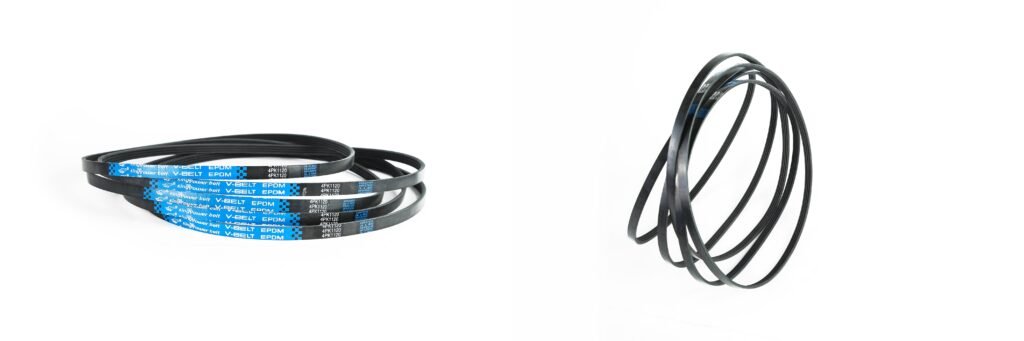
2. Polyester Fiber Belts
Polyester fiber belts are made from a combination of polyester fabric and rubber, offering high strength, wear resistance, and corrosion resistance. These belts are ideal for long-distance conveying tasks in harsh environments such as mining and ports. They can withstand high tension and impact forces. The wear resistance of polyester fiber belts is particularly outstanding, significantly extending their service life and reducing maintenance costs.
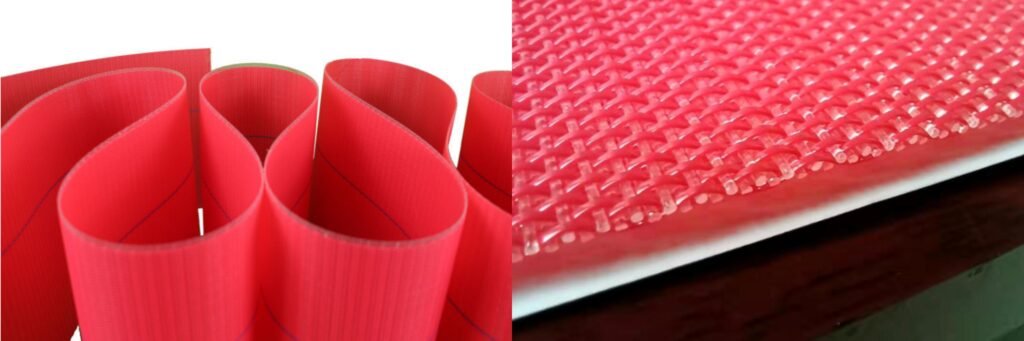
3. Nylon Belts
Nylon belts are made from nylon fabric and rubber composites, providing high strength, wear resistance, and corrosion resistance. These belts are suitable for medium-to-long-distance conveying in industries such as coal mining and construction materials. They maintain stable performance even under harsh working conditions. Nylon belts have a high tensile strength, effectively preventing safety issues such as breakage.
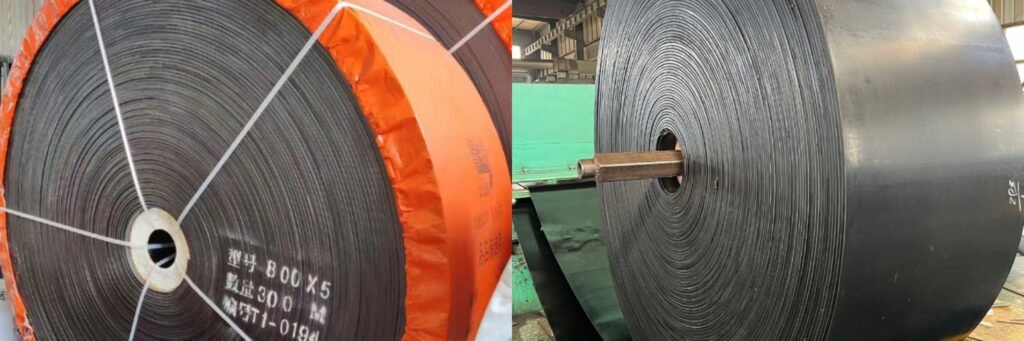
4. Metal Mesh Belts
Metal mesh belts are made from woven metal wires and are characterized by their high-temperature and corrosion resistance. They are particularly suitable for high-temperature environments like sintering furnaces and coke ovens. Metal mesh belts not only withstand high temperatures but also maintain structural stability, able to bear heavy loads and impact forces, making them the ideal choice for material conveying in high-temperature environments.

Classification by Purpose
1. Conveyor Belts
Conveyor belts are primarily used for material transportation and are one of the most common types of industrial belts. Depending on the material being conveyed, conveyor belts can be divided into various types, including rubber conveyor belts, polyester conveyor belts, and nylon conveyor belts. Additionally, there are special-purpose conveyor belts for oil resistance, acid-alkali resistance, and high-temperature resistance to meet the needs of different industries. Conveyor belts are typically used in a looped configuration, offering well-designed, appropriately colored, lightweight, and durable features.
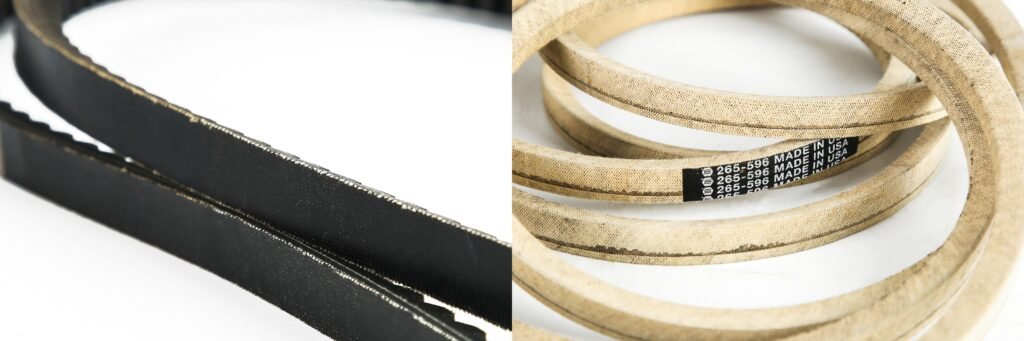
2. Transmission Belts
Transmission belts are used for power transmission and are widely used in various mechanical equipment. Common types of transmission belts include V-belts, toothed belts, and pulley belts. The V-belt (also known as the triangle belt) is the most common transmission belt, known for its simple structure, easy manufacturing, installation, and maintenance. Toothed belts transmit power through the engagement of the teeth on the belt and the grooves on the pulley, offering accurate transmission ratios, compact structure, and resistance to oil and wear. The choice of transmission belt depends on the specific transmission method and power requirements.
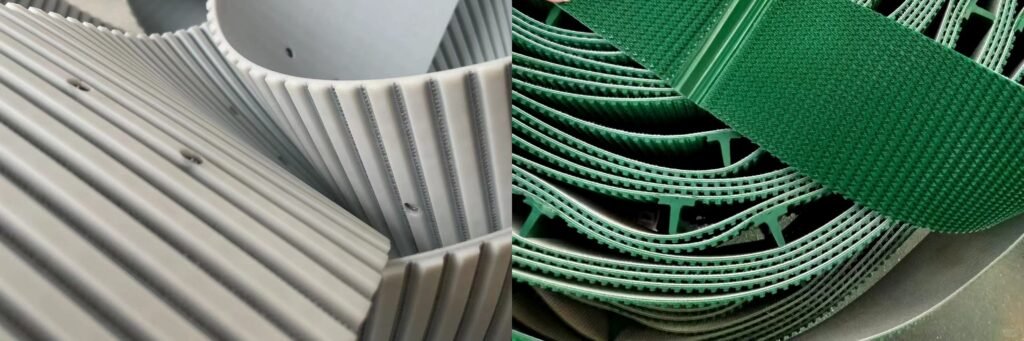